1.Nano Drug Carrying Emulsion System
Designed for dissolvable of API preparation in the areas of nano particle size emulsion and suspension. the automatic solution preparation system can effectively eliminate the risk of cross contamination and product contamination during preparation, thereby improving the productivity and reliability of product; every detail is carefully designed based on the latest GMP, FDA to match the actual production requirements. requirement with optimal designing.
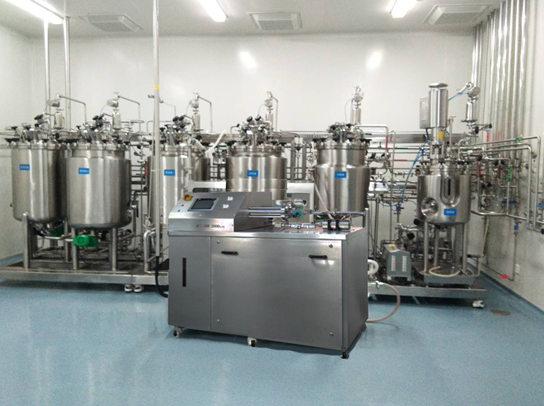
Principal features of the system:
1.Sterilizing design and no dead angle, moving area minimize residues
2.SIEMENS PLC touch screen: one-touch operation; concrete and clear process flow diagram; fully automatic solution ,preparation and material transfer simple, convenient and user-friendly
3.Automatic CIP and SIP system enable automatic in-process SIP and CIP, which helps to reduce the production costs and labor intensity
4.Automatic in-processing inspection of filter integrity
5.Automatic in-processing real-time monitoring of weighing, and automatic setting of constant volume
6.Automatic real-time recording and printing of various related data
2.Nano Liposome Extrusion System
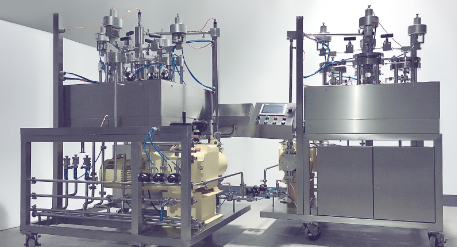
Characters:
1. Various microporous membranes enable the liposome particle size and its
distribution to be controllable. Membrane size available:
250nm,200nm,180nm,150nm,100nm,80nm,50nm…etc.
2. The temperature is controllable with pipe jacket, which was filled with
thermostatic water.
3. The liposome handling efficiency is depended on the flow rate of diaphragm
pump, which contributes to high speed.
4. The contact portion of liposome is made of forged stainless steel 316L.
5. The uniform microporous sheet was electroformed from nickel sheet is smoothly,
flat, and resistant to high pressure.
6. At the liposome contact portion, Ra<0.4μm;
electro-polished.
Diameter of extruding membrane: 50mm,76mm,90mm,142mm,293mm,
Maximum design pressure: 70 bar
3.Sterile API Jetmill system
With the growth of pharmaceutical industry in the world, sterile API pulverizing systems increasing attractive attention, and enjoy constantly extensive applications. Designed for sterilizing API pulverizing process, this complete set of system incorporates the equipment for the discharge, conveyance, pulverization (whole grain), re-conveyance, mixing and metering, etc. of dry sterile APIs.
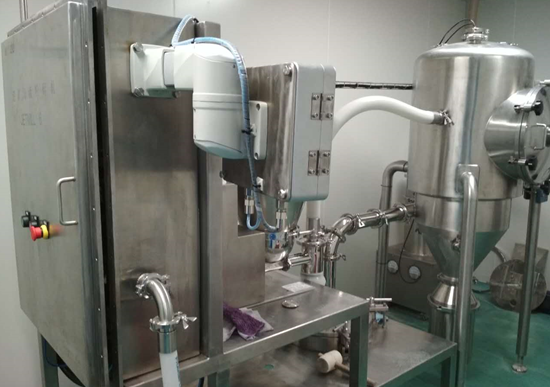
1.The production is performed under completely airtight conditions to minimize the hazards for operator.
2.Effectively alleviate the risk of product contamination by particles and microorganisms.
3.The latest GMP-compliant system assures production safety.
4.Materials are transferred and handled throughout the technological process in a closed environment or dynamic level-A environment.
4.Isolating System for Jetmill
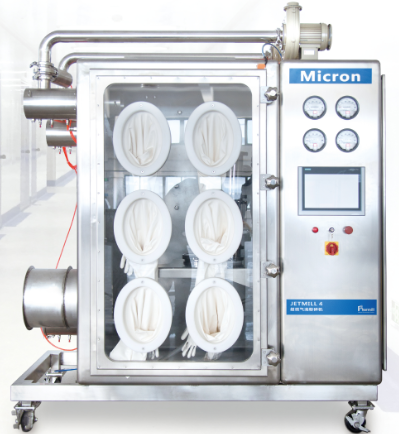
Characters
of jetmill +isolator:
1\The portion in direct contact with material is completely made from 316L stainless steel, and its surface is polished until RA≤0.25μm
1.The surface of contact the API is completely made from SS316L , and its surface is polished until RA≤0.25μm
2.Other metal portions are made from SS316, and their surfaces are polished until RA≤0.8μm
3.The contact portion of visual glass is made from borosilicate
4.The gasket in contact with product is made from PEEK or PTFE
5.The washer in contact with product is made from EPDM or PTFE
6.Ambient temperature: 0~40℃ Operating temperature: 0~50℃