Verification Service
Verification Service
Noozle Fluid has a specialized verification service team established to verify pharmaceutical water equipment, solution preparation process system, clean piping system, and high-pressure gas.
Noozle Fluid has a specialized verification service team established to verify pharmaceutical water equipment, solution preparation process system, clean piping system, and high-pressure gas.
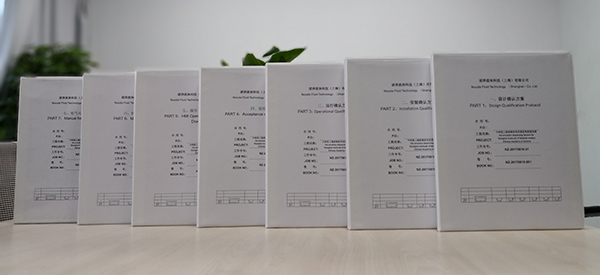
The life cycle of verification starts from the formulation of URS; after design qualification, construction, installation qualification and transportation qualification, the performance qualification is performed to check whether URS is completed.
Verification means to establish written evidence that assures the compliance with the quality characteristics pre-defined by customer.
DQ (design qualification): The validation of project or system design and selection, including the validation of standards and supporting documents used for design and selection, and the information provided by supplier.
Note: Standard equipment of which the type selection qualification is performed based on user’s requirements can be exempted from design qualification. Design qualification must demonstrate that the design documents fully comply with user's requirements. Design documents, drawings and technical specifications shall measure up to the technical terms of purchase contract.
IQ (installation qualification): Installation qualification principally includes, but not limited to the following items:
1. Out of box audit:
Check whether the content is consistent with packing list;
Visual inspection: Check whether the equipment for damage and corrosion;
Identification inspection: Check whether all kinds of labels on the equipment (name, model, manufacturer, serial number, equipment item number, etc.) comply with design requirements;
Check whether the documents required to be provided by the manufacturer/supplier are complete;
2. Validation of Installation Environment
Check whether the equipment is suitable for the installation environment and compliant with requirements of pharmaceutical manufacturing. GMP specifies the cleanliness level, temperature and relative humidity, as well as ventilation and dust removal requirements for factory buildings where different types of equipment are located.
Utility system inspection, for example, of the connections and parameters of water, electricity, compressed air, steam, process vacuum, and vacuum dust removal.
3. Installation Qualification
Check the list, parameters, installation locations and calibration records of instruments and meters,
Validate the installation of computer/program controlled system, and check the initial parameters adjustment for control system.
Check the motor and pump parameters (model, serial number, direction of operation, etc.).
Piping pressure test, pickling & passivation test, and test reports.
As-built drawing.
Installation of ancillary equipment and mobile equipment associated with this equipment, e.g. supporting platform, storage tank, buffer tank, weighing instrument, etc.
OQ (operation qualification): Primary coverage of operation qualification:
1. Applicability of SOP draft;
2. Reliability of external conditions for operation;
3. Accuracy of instrument display;
4. Fluctuation of equipment operating parameters;
5. Stability and safety of equipment operation;
Note: Upon the completion of equipment installation qualification, it is important to, based on the draft standard operating procedures (SOP), perform adequate no-load tests for each part and the whole of equipment to check the applicability of draft SOP, the fluctuation of equipment operation parameters, the reliability of instruments, and the operation stability of equipment so as to ensure that the equipment can function accurately within the specified range and meet the defined technical index. In this process, it may be necessary to supplement and modify the SOP appropriately and adjust the equipment to a certain extent (the verification team shall analyze all the collected and summarized data, give comments, and submit the data to leaders concerned for review and approval).
PQ (performance qualification): Performance qualification is the trial production performed under simulated actual operating conditions. Blank material is normally used for test run to preliminarily determine the applicability of equipment. The qualification batch could be determined by characteristics of product and equipment. If the equipment is confirmed to run stably and meet the requirements of production process, the verification team will summarize and submit relevant data to the leaders concerned for review and approval, and then the equipment can be brought into continuous operation.
Verification means to establish written evidence that assures the compliance with the quality characteristics pre-defined by customer.
DQ (design qualification): The validation of project or system design and selection, including the validation of standards and supporting documents used for design and selection, and the information provided by supplier.
Note: Standard equipment of which the type selection qualification is performed based on user’s requirements can be exempted from design qualification. Design qualification must demonstrate that the design documents fully comply with user's requirements. Design documents, drawings and technical specifications shall measure up to the technical terms of purchase contract.
IQ (installation qualification): Installation qualification principally includes, but not limited to the following items:
1. Out of box audit:
Check whether the content is consistent with packing list;
Visual inspection: Check whether the equipment for damage and corrosion;
Identification inspection: Check whether all kinds of labels on the equipment (name, model, manufacturer, serial number, equipment item number, etc.) comply with design requirements;
Check whether the documents required to be provided by the manufacturer/supplier are complete;
2. Validation of Installation Environment
Check whether the equipment is suitable for the installation environment and compliant with requirements of pharmaceutical manufacturing. GMP specifies the cleanliness level, temperature and relative humidity, as well as ventilation and dust removal requirements for factory buildings where different types of equipment are located.
Utility system inspection, for example, of the connections and parameters of water, electricity, compressed air, steam, process vacuum, and vacuum dust removal.
3. Installation Qualification
Check the list, parameters, installation locations and calibration records of instruments and meters,
Validate the installation of computer/program controlled system, and check the initial parameters adjustment for control system.
Check the motor and pump parameters (model, serial number, direction of operation, etc.).
Piping pressure test, pickling & passivation test, and test reports.
As-built drawing.
Installation of ancillary equipment and mobile equipment associated with this equipment, e.g. supporting platform, storage tank, buffer tank, weighing instrument, etc.
OQ (operation qualification): Primary coverage of operation qualification:
1. Applicability of SOP draft;
2. Reliability of external conditions for operation;
3. Accuracy of instrument display;
4. Fluctuation of equipment operating parameters;
5. Stability and safety of equipment operation;
Note: Upon the completion of equipment installation qualification, it is important to, based on the draft standard operating procedures (SOP), perform adequate no-load tests for each part and the whole of equipment to check the applicability of draft SOP, the fluctuation of equipment operation parameters, the reliability of instruments, and the operation stability of equipment so as to ensure that the equipment can function accurately within the specified range and meet the defined technical index. In this process, it may be necessary to supplement and modify the SOP appropriately and adjust the equipment to a certain extent (the verification team shall analyze all the collected and summarized data, give comments, and submit the data to leaders concerned for review and approval).
PQ (performance qualification): Performance qualification is the trial production performed under simulated actual operating conditions. Blank material is normally used for test run to preliminarily determine the applicability of equipment. The qualification batch could be determined by characteristics of product and equipment. If the equipment is confirmed to run stably and meet the requirements of production process, the verification team will summarize and submit relevant data to the leaders concerned for review and approval, and then the equipment can be brought into continuous operation.